Linear process flow diagrams
The simplest form of process flow diagram is linear. The key steps in the process are identified, laid out step by step, and subsequently verified by the HACCP team.
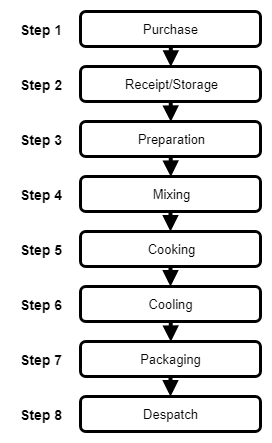
The diagram shows a simple 8-step process, where one step follows the next in order:
- Step 1: Purchase
- Step 2: Receipt/Storage
- Step 3: Preparation
- Step 4: Mixing
- Step 5: Cooking
- Step 6: Cooling
- Step 7: Packaging
- Step 8: Despatch
Additional steps
Additional steps may be identified during the verification process and these should be added into the process flow diagram.
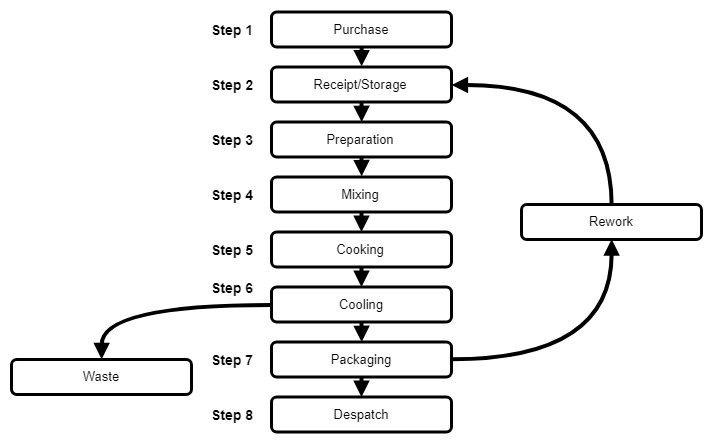
The diagram shows the same 8-step process as in the previous diagram, but with two new options added.
- From step 6, which is “Cooling”, the process could proceed to 'Waste', instead of to Step 7, Packaging.
- From Step 7, Packaging, the process could move to a new 'Rework' step and then go back to Step 2, Receipt/Storage, instead of moving on to Step 8, Despatch.
Modular HACCP plans
These can be used for more complex food operations or in situations where several different foods are produced by the same business which share certain parts of the production process. You would create a diagram showing the modules in your overall process, and then additional diagrams showing the steps of the process within each module.
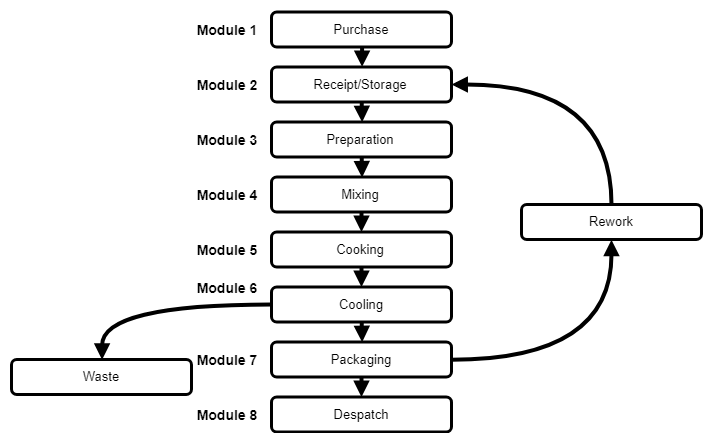
This diagram looks the same as the previous one, showing the linear process with 'Rework' and 'Waste' options added, except that the boxes are marked as Modules rather than Steps. This indicates that each module, such as Module 1: Purchase or Module 5: Cooking, would have a diagram showing the steps of that process.
If you have multiple products, and some of the processes you go through with different products work in the same way (for example, if you package or store several different products in the same way) you can refer to one shared diagram for the module, rather than making different ones. That way, you don’t have to update several different plans or diagrams if something in the shared process changes.
Diagrams for single modules
This diagram is an example of how you might show the process for Module 2 in the previous diagram, the 'Receipt' process.
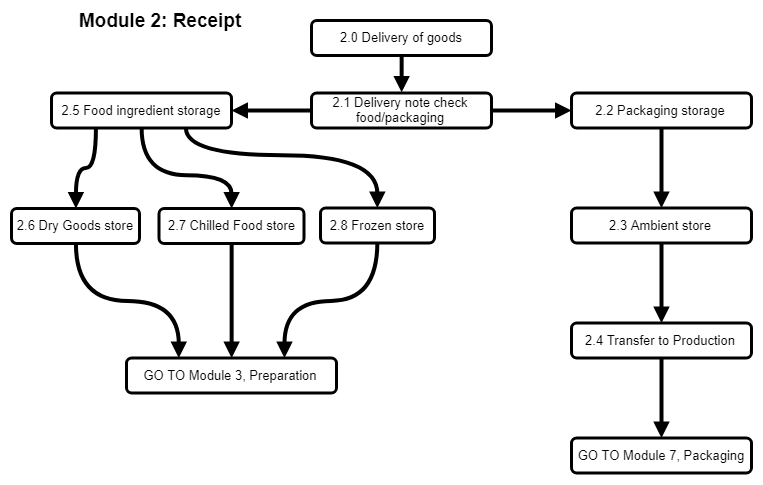
This diagram is headed 'Module 2: Receipt' and it shows a process with steps numbered from 2.0 to 2.8.
The starting point is Step 2.0, Delivery of goods.
The process moves to Step 2.1, Delivery note check food/packaging.
From there, the process moves to either 2.2, packaging storage, or 2.5, Food ingredient storage.
The packaging part of the process has the following steps:
- 2.2, packaging storage
- 2.3, ambient storage
- 2.4, Transfer to production
After that, the diagram shows that you move to Module 7, Packaging, which would be presented in a different diagram.
The food ingredient part of the process goes from step 2.5, Food ingredient storage, to one of three options. These are:
- 2.6, Dry goods store
- 2.7, Chilled food store
- 2.8, Frozen store
From any of those three options, the diagram shows that you then move on to Module 3, Preparation, which would be presented in a different diagram.